Проработка вопросов повышения качества зубчатых колес
Секция: Технические науки
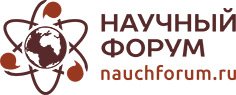
XLVI Студенческая международная заочная научно-практическая конференция «Молодежный научный форум: технические и математические науки»
Проработка вопросов повышения качества зубчатых колес
Статья посвящена улучшению качества изделия «Блок зубчатых колес» и совершенствованию условий его производства. К блокам зубчатых колес (производитель Саратовский агрегатный завод АО «САЗ») предъявляются повышенные требования точности и надежности в виду важного положения, занимаемого в узлах. Были разработаны меры по повышению качества получаемых изделий. Для этих целей были произведены замена материала и модернизация установочно-зажимного приспособления.
Зубчатой передачей называется механизм, служащий для передачи вращательного движения с одного вала на другой и изменения частоты вращения посредством зубчатых колес и реек.
Зубчатые передачи представляют собой наиболее распространенный вид передач в современном машиностроении. Они очень надежны в работе, обеспечивают постоянство передаточного числа, компактны, имеют высокий КПД, просты в эксплуатации, долговечны и могут передавать любую мощность (до 36 тыс. кВт).
К недостаткам зубчатых передач следует отнести: необходимость высокой точности изготовления и монтажа, шум при работе со значительными скоростями, невозможность бесступенчатого изменения передаточного числа.
В связи с разнообразием условий эксплуатации формы элементов зубчатых зацеплений и конструкции передач весьма разнообразны.
В качестве объекта модернизации выберем блок прямых цилиндрических зубчатых колес.
Этот выбор обусловлен важным положением, занимаемым данной деталью в сборочном узле, и повышенными нагрузками, что подразумевает более тщательную проработку конструкции для повышения надежности и долговечности.
Данная деталь входит в состав переводного редуктора и является частью механизма подъема высоконагруженного узла. Крепление блока к валу происходит при помощи конических штифтов 3х16 ГОСТ 3129-70. Штифты кернятся в 2-3х точках. Смазочно-промывочными материалами являются ЛИТОЛ-24 ГОСТ 21150-87 и бензин БР-1 ГОСТ 443-76. Условия работы блока зависят от скорости двигателя и состояния зубьев как самого блока, так и сопряженных с ним колес. Контроль параметров производится в процессе изготовления до нарезания зубьев.
Изготовление зубьев осуществляется на фрезерном станке Samputensili S140 и на зубодолбежном станке 5122, в ходе которых были выявлены следующие проблемы:
1) При повышении режимов резания на зубофрезерной операции и числа двойных ходов долбяка материал блока зубчатых колес начинает крошиться, что приводит к ухудшению качества изготовления.
2) Неточности базирования могут привести к отклонению от круглости и радиальному биению, приводящему к необратимому браку изделия.
Анализ конструкции изделия позволил определить основные направления ее совершенствования:
1) Изменение материала детали (блока зубчатых колес).
2) Улучшение/модификация базирующего приспособления.
3) Разработка конструкторско-технологических мероприятий, обеспечивающих качество изготовления детали.
Блок зубчатых колес подвергается переменной нагрузке, что приводит к регулярным ударным напряжениям через неравные промежутки времени. Сталь 40Х после термообработки приобрела высокую прочность, но и хрупкость возросла пропорционально, в следствии чего существует риск нарушения целостности конструкции и зацепления. В качестве материала-заменителя стали 40Х для детали предлагается среднелегированная сталь 30ХГСА. Этот выбор основан на особенностях функционирования детали в сборочной единице и свойствами выбранной стали. Сталь 30ХГСА за счет легирующих элементов и достаточно большого содержания углерода обладает высокой прочностью в сочетании с повышенными специальными свойствами при достаточном уровне пластичности и стойкости против хрупкого разрушения.
Описание конструкции и принципа работы разрабатываемого приспособления. На предприятии данную сборочную операцию выполняют при помощи приспособления – оправки П-3, закрепленной в центрах:
Рисунок 1. Приспособление П-3
Деталь устанавливается в оправку. Оправка наворачивается на нижний неподвижный центр, затем прижимается верхним центром, непосредственно к которому крепится поршень пневмоцилиндра. Зажим детали происходит при подаче воздуха в верхнюю полость пневмоцилиндра, при этом центр движется вниз. Разжим совершается подачей воздуха в нижнюю полость пневмоцилиндра и возвращением поршня обратно. Для контроля количества воздуха используем компрессор.
Расчёт диаметра пневмопривода. Заготовка установлена и закреплена в приспособлении. На заготовку действует окружная сила резания.
Уравнение равновесия будет иметь вид:
где: PZ = окружная сила резания
К – коэффициент запаса
fОП = 0,16...0,8 – коэффициент трения на опорах ;
fОП = 0,16...0,8 - коэффициент трения в центрах
Определяем диаметр цилиндра , распишем Q:
– давление системы(0,4МПа)
По ГОСТ 15608-81 принимаем ближайшее стандартное значение
D = 25 мм
Расчёт слабого элемента. В качестве слабого звена принимаем шток и рассчитаем шток на сжатие. Диаметр штока d = 12 мм. Материал штока – сталь 20 ГОСТ 1050-74, = 115 Мпа. Сила на штоке Р=1000 Н.
Расчетный диаметр штока
Таким образом, d < dp; прочность штока удовлетворительна.
Улучшение качества изготовления детали. В базовом варианте заводского технологического процесса изготовление зубчатого венца исследуемой детали происходит на станке HAMAI-120 за 2 операции: зубофрезерование и зубошевингование. Это приводит к неминуемым погрешностям, возникающим из-за неоднократных установов и положений инструментов. В перспективном технологическом процессе применяется зубофрезерный станок S140. Помимо перспективной конструкции и программного обеспечения станка, на нем возможно изготовить зубчатый венец за один установ и одним инструментом без ухудшения точности детали.
Заключение. Выполненные улучшения и расчеты позволяют изготовлять более технологичные и надежные по сравнению с аналогами блоки зубчатых колес без координальной переработки производственных технологических процессов и небольшими денежными затратами на модернизацию и эксплуатацию средств технологического оснащения.
