Совершенствование технологии изготовления тонкостенных цилиндрических деталей
Журнал: Научный журнал «Студенческий форум» выпуск №14(150)
Рубрика: Технические науки
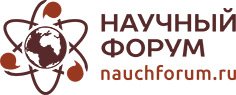
Научный журнал «Студенческий форум» выпуск №14(150)
Совершенствование технологии изготовления тонкостенных цилиндрических деталей
Аннотация. В данной работе были рассмотрены методы обработки металлических заготовок давлением. Проведены исследования совершенствования технологии изготовления тонкостенных цилиндрических деталей, позволившие прийти к выводу, что использование метода ротационной вытяжки цилиндрических заготовок имеет достаточно большой потенциал в виду меньшего объёма трудозатрат по сравнению с другими методами вытяжки. Были проанализированы методы обработки стальных заготовок ротационной вытяжкой, а также схемы обработки, применяемые в современном производстве.
Ключевые слова: технологические процессы, детали, ротационная вытяжка, методы обработки, производство, ролики.
Возрастающая необходимость в изготовлении ТЦД, наравне с требуемые от них высоких показателей точности геометрических форм, размерам диаметров, тонкостенности детали, качеству поверхностей деталей и механическим свойствам, связанными с обеспечиванием долговечности эксплуатации деталей в условиях агрессивной среды, больших температур и давлений, даёт ясно понять о необходимости улучшения способов их производства.
Наряду с классическими способами производства ТЦД обработкой давлением и многооперационной вытяжкой, за последние пару лет обширное употребление обретает ротационная вытяжка на специальном станке с применением в качестве деформирующих инструментов роликов.
Ротационную вытяжка – это процесс пластичного деформирования оболочечной детали из стальной заготовки. Крутящиеся оправки вместе с роликами из плоской или полой вращающейся заготовки формируют симметричную или не симметричную по оси деталь.
Готовая деталь принимает ту же форму, что и крутящаяся оправка.
Подбор схемы РВ устанавливается конструктивными особенностями производимых деталей, технологическими способностями применяемой техники и качествами обрабатываемого металла.
Применение той или другой схемы преследует задачу создать самые подходящие условия для деформации, обеспечивающие приобретение установленных высококачественных характеристик и геометрической формы изготавливаемых деталей (рисунок 1.1) при большой производительности процесса.
Рисунок 1.1. Типовые конструкций тонкостенных цилиндрических деталей
Методы обработки цилиндрических заготовок ротационной вытяжкой делятся на два: прямой и обратный (рисунок 1.2). При прямом методе (рисунок 1.2 - а) деталь закрепляется со стороны фронтального торца (в самом начале металлообработки). Во время РВ по этому методу часть детали, прошедшая обработку, растягивается, а необработанная часть детали свободна от напряжений и при утончении стенки передвигается вдоль оправки.
При обратном методе (рисунок 1.2 - б) деталь закрепляется на оправку до упора задним торцом в бортик оправки. Во время металлообработки ещё не подвергнувшаяся деформации часть детали принимает осевую силу деформирования, а обработанная сторона заготовки плавно двигается по оправке, испытывая только остаточные напряжения, которое содействует изменению ее конструктивной формы.
Вследствие этого обратный метод выделяется более малыми возможностями обеспечивания точных характеристик и используется только для деталей с низкими характеристиками по качеству создаваемой детали. Производство деталей с завышенными характеристиками производят в основном по прямому методу. [1]
Рисунок 1.2. Методы РВ цилиндрических тонкостенных деталей: а - прямой метод; б - обратный метод: 1 - ролик; 2 - заготовка; 3 - оправка
Схемы обработки ротационной вытяжкой применяемые в современном производстве классифицируются как однороликовые и многолирование, в зависимости от числа деформационных роликов.
Схемы РВ с одним и двумя роликами (рисунок 1.2) применяются в основном при производстве не длинных деталей, так как вышеуказанные схемы могут привести к смещению оси оправки относительно оси заготовки во время обработки, что наталкивает на снижение точных параметров производимых деталей.
Вследствие этого для производства длинных деталей с соотношением L/D ≥ 5 в наибольшей степени обширное использование находят трехроликовые схемы РВ, располагающиеся равномерно через каждые 120° по длине окружности. Применение схем с тремя роликами формирует условия для равновесия сил деформирования, которое помогает освободить шпиндель станка от влияния радиальных нагрузок и сводит на нет возможность прогиба оправки с заготовкой во время металлообработки.
Наравне со схемами с тремя роликами на производстве благополучно используются четырехроликовые схемы РВ. При применении схем с множеством роликов, в целях получения самых подходящих условий деформации, взаимное размещение роликов, а также их размещение относительно оправки, могут различаться. Вследствие этого вышеуказанные схемы подразделяются на несколько вариаций.
Наравне с вышеупомянутыми схемами, иностранными компаниями и отечественными предприятиями, сконструированы и сыскивают удачно использование схемы РВ с разделенной зоной деформации.
Такого рода схемы предрасполагают рядом весомых преимуществ, таких как уменьшение потребляемых деформирующих сил РВ, а также достижение больших степеней деформирования за один проход, что даёт возможность увеличить интенсивность процесса РВ. Главное в вышеуказанных схемах то, что общая деформация распределяется среди роликов по определенной зависимости (рис. 1.3).
Распределение деформации происходит при помощи обоюдного перемещения роликов по оси и радиальном направлении, или перемещением лишь в радиальном направлении, при всем при этом применяются ролики с разнообразными профилями. [2]
Рисунок 1.3. Схема РВ цилиндрических тонкостенных деталей с тремя роликами и с распределением деформации при радиальном перемещении роликов: 1 - ролик; 2 - оправка; 3 – заготовка
Исследование схем РВ, применяемых в производстве, даёт возможность прийти к последующим выводам.
Однороликовые или двухроликовые схемы РВ целенаправленно применять при производстве не длинных деталей с соотношением длины к диаметру не больше 2-3.
При большем соотношении длины к диаметру преимущественно лучше применять трехроликовые или четырехроликовые схемы РВ, дающие возможность сбалансировать радиальные силы деформации и, таким образом, исключить вероятность смещения оправки во время металлообработки деталей.
Схемы РВ с открытой калибровкой, не обеспечивающие регулировку наплыва материала во время металлообработки, располагают ограниченными возможностями в плане достижения высококачественных параметров деталей и высокопроизводительных процессов. Связано это с тем, что ограничения увеличения наплыва при заданных схемах РВ можно достигнуть при помощи понижения объёма рабочей подачи S и угла рабочего конуса ролика для пластичных металлов,
- для прочных металлов.
Схемы РВ с закрытой калибровкой помогают регулировать объём наплыва в большом спектре режимов металлообработки и обеспечивают намного подходящие условия деформирования для достижения высококачественных параметров создаваемых деталей и увеличения высокопроизводительных процессов. Но при всем при этом, закрытая калибровка осуществляет утончение стенки детали с неизменной величиной , почти равная величине гребня ролика
, что даёт возможность применять эту схему РВ лишь для заготовок с постоянной толщиной стенки.
Схемы РВ с распределением деформации обладают огромными технологическими возможностями, потому как перемена в отношении углов рабочего конуса роликов в комплекте, величина обоюдного радиального и осевого перемещений роликов помогают создать самые подходящие условия деформации для достижения высочайшей точности как отдельных характеристик детали, так и комплекта заданных требований. Наличествование вышеуказанных преимуществ формирует предпосылки для широкого использования схем РВ с распределением деформации при производстве деталей с разными типоразмерами, как с неизменной, так и с переменной толщиной стенки из разнообразных металлов.
