Повышение качества обработки деталей методом поверхностного пластического деформирования
Секция: Технические науки
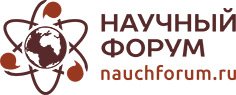
XX Студенческая международная научно-практическая конференция «Технические и математические науки. Студенческий научный форум»
Повышение качества обработки деталей методом поверхностного пластического деформирования
К современной продукции машиностроительного производства предъявляют всё более жёсткие требования по долговечности, надёжности и качеству выпускаемых изделий. Повышение качества обработки деталей является актуальной задачей машиностроения. Эта задача может решаться путем внедрения и применения новых конструкционных материалов, методов обработки. К таким методам относятся методы обработки поверхностным пластическим деформированием (ППД).
В последнее время данные методы являются наиболее распространенными видами упрочняющей обработки на этапах финишной обработки.
Они имеют широкие технологические возможности, что способствует обрабатывать детали любого вида, обеспечивать высокое качество поверхностного слоя и повышать долговечность деталей машин.
Плюсы методов обработки поверхностным пластическим деформированием заключаются в следующем:
- Повышение твердости поверхности
- Повышение износостойкости деталей
- Повышение сопротивления схватывания
- Увеличения предела выносливости детали
- Уменьшения шероховатости поверхности
Существуют различные методы обработки ППД, которые можно разделить на 2 группы.
- Ударные
- Статические.
К основным статическим методам можно отнести:
- Накатывание. Накатывание подразделяется на раскатывание (для внутренних поверхностей) и обкатывание (для плоских и выпуклых поверхностей). Сущность метода заключается в качении инструмента (шар, ролик) по обрабатываемой поверхности. Применяются стандартные инструменты различной конфигурации, изготавливаемые из сталей 18ХВГ, Р18, ШХ15, Р6М5 и другие.
- Выглаживание. При этом методе происходит скольжение инструмента по поверхности материала. Инструментом являются наконечники различной конструкции, изготавливаемые из сверхтвердых материалов или алмаза. Алмазное выглаживание — наиболее популярный процесс в машиностроении. Его отличием является малый радиус профиля (0,5 ….4 мм) и высокая твердость инструментов, что позволяет осуществить деформирование поверхностного слоя металла с минимальными затратами сил.
- Вибрационное накатывание. При вибрации инструмента по касательной к плоским поверхностям деформируемого металла осуществляется накатывание или выглаживание. Инструментом являются стальные закаленные шарики. Основной задачей данного метода являются повышение стойкости, гидроплотности, увеличение жесткости материалов и др.
- Поверхностное дорнование. При этом методе происходит поступательное скольжение дорна по охватывающей его поверхности.
К ударным методам относятся:
- Дробеструйная обработка. Сущность процесса заключается в воздействии дроби на различные поверхности. Источником воздействия является подаваемый на большой скорости воздушный поток. К плюсам данного метода можно отнести возможность качественного упрочнения деталей различной формы, которые имеют мелкие пазы, галтели или надрезы.
- Центробежно-ударная обработка. Метод заключается в деформации обрабатываемой поверхности на определенную глубину многочисленными ударами от роликов или шариков, помещенных в радиальные пазы быстро вращающегося диска. Таким способом можно обработать плоские и фасонные поверхности деталей из цветных и черных металлов
Количество способов поверхностного пластического деформирования многообразно, они все хорошо изучены и каждый из них имеет собственную технологическую сферу. На практике они внедрены в основном в мелкосерийное производство для ответственных деталей.
Возможно заменять финишные процессы, например тонкого точения, шлифования или полирования с охлаждением на методы поверхностного пластического деформирования без применения смазочно-охлаждающих средств, но среди известных методов ППД очень трудно найти технологический процесс, который удовлетворял бы требованиям массового производства.
Когда за быстрое время - до 20 с необходимо выполнить требования к процессу и качеству обработки детали.
