АНАЛИЗ ОПТИМАЛЬНЫХ РЕЖИМОВ ПЛАЗМЕННОЙ ОБРАБОТКИ СТАЛИ 65Г
Конференция: LXXXIII Международная научно-практическая конференция «Научный форум: технические и физико-математические науки»
Секция: Металлургия и материаловедение
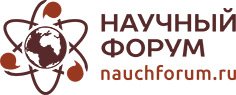
LXXXIII Международная научно-практическая конференция «Научный форум: технические и физико-математические науки»
АНАЛИЗ ОПТИМАЛЬНЫХ РЕЖИМОВ ПЛАЗМЕННОЙ ОБРАБОТКИ СТАЛИ 65Г
Аннотация. В данной статье представлен способ выбора оптимальных режимов плазменной обработки стали 65Г, таких как глубина и ширина зоны закалки, скорость движения, определяющая производительность процесса, погонная энергия и скорость охлаждения в зоне закалки. Приведен анализ изменения параметров закалки в зависимости от диаметра плазмообразующего сопла, что может привести к уменьшению или увеличению глубины и ширины зоны закалки, скорости движения и погонной энергии, что соответственно может образовать накопление дефектов структуры и зарождение очага разрушения.
Abstract. This article presents a method for selecting the optimal modes of plasma treatment of the surface of steel 65G, such as the depth and width of the hardening zone, the speed of movement, which determines the productivity of the process, the heat input and the cooling rate in the hardening zone. An analysis is given of the change in the hardening parameters depending on the diameter of the plasma-forming nozzle, which can lead to a decrease or increase in the depth and width of the hardening zone, the speed of movement and heat input, which, accordingly, can form the accumulation of structural defects and the nucleation of a fracture site.
Ключевые слова: плазменная обработка, износостойкость, плазмообразующее сопло, глубина и ширина зоны закалки, градиентное нанесение.
Keywords: plasma treatment, wear resistance, plasma-forming nozzle, depth and width of the hardening zone, gradient application.
Общеизвестно, что в настоящее время до 90 % машин и механизмов выходят из строя не из-за поломок деталей, а вследствие изнашивания их рабочих поверхностей, поэтому основным требованием к структуре и свойствам поверхностного слоя деталей и изделий является хорошая износостойкость.
При объемном нагружении процессы пластической деформации локализуются в определенной части объема материала, где и происходит накопление дефектов структуры, концентрация напряжений и зарождение очага разрушения, в то время как процессы пластической деформации и разрушения поверхностных слоев отличаются в первую очередь сложным распределением напряжений по всей зоне контакта.
Расчет максимальных размеров зоны закалки
Глубина и ширина зоны закалки должны определяться с учетом двух факторов (рис.1):
- температура нагрева в каждой точке зоны закалки должна быть равной или больше критической для данного материала T ≥ Tзак;
- скорость охлаждения в каждой точке хвостовой части изотермы Tзак должна быть не меньше критической скорости охлаждения для данной стали (как видно на рис. 4.4, поскольку c2 > c1, то имеем скорость охлаждения vохл2 < vохл1, а значит, если в точке 1 скорость охлаждения vохл не меньше критической vкр (например, для стали 65Г vохл = vкр = 100 K/c), то глубина этой точки будет соответствовать максимальной глубине закалки hзак.max):
vохл = dT/dt = (T – T зак)˖v/c.
Аналогично рассчитывается максимальная ширина закалки bзак.max.
Рисунок 1. Схема расчета максимальной глубины закалки, где T → T зак.
Выбор оптимальных режимов плазменной закалки
С целью предупреждения роста зерна, окисления или подплавления закаливаемой поверхности необходимо при расчете режима закалки ограничивать максимальную температуру поверхности металла [1, с. 217].
Рисунок 2 иллюстрирует влияние тока сжатой дуги и диаметра плазмообразующего сопла на перечисленные выше параметры.
Рисунок 2. Зависимость глубины зоны закалки от тока сжатой дуги (dсч = 3 мм; s = 20 мм)
Можно выделить две области возможных режимов плазменной закалки, условно названных «Мягкие режимы» и «Жесткие режимы». В области мягких режимов, характерных для относительно малых токов сжатой дуги и небольших скоростей движения, размеры зоны закалки лимитирует скорость охлаждения металла; температура поверхности закаливаемого металла ниже задаваемой допустимой температуры (естественно, меньшей температуры плавления для исключения последующих операций шлифовки закаленных поверхностей).
В области жестких режимов, характерных для повышенных токов сжатой дуги и больших скоростей движения, размеры зоны закалки лимитируются температурой поверхности закаливаемого металла, которая не должна превышать заданную допустимую температуру. Скорости охлаждения металла в зоне закалки при этом выше критической л скорости охлаждения, необходимой для данного материала.
К числу входных параметров технологической системы относятся параметры плазменной обработки, движения детали или плазматрона, параметры обрабатываемого материала (рис.1).
Параметры плазменной обработки являются переменными. Благодаря им можно значительно варьировать характеристики технологического процесса. Параметры плазменной обработки включают в себя характеристики подводимого к плазматрону тока, плазмообразующего газа и водяного охлаждения.
Сила тока I определяет эффективную тепловую мощность плазменной струи q:
q = 0,24 η п.н. I U, (7)
где - η п.н КПД плазменного нагрева, η п. н – η п η с, η п – КПД плазмотрона, η с – КПД плазменной струи с учетом потерь на излучение и отражение, U –напряжение на дуге.
Расход плазмообразующего газа должен обеспечивать стабильное плазмообразование, а также стабилизацию дуги в канале плазматрона.
От марки плазмообразующего газа зависит температура плазмы. Инертные газы обеспечивают защиту внутреннего канала плазматрона от окисления, а обрабатываемой поверхности – от окисления и выгорания легирующих элементов. Увеличение силы тока и расхода плазмообразующего газа ведет к увеличению твердости и глубины упрочненного слоя. Это объясняется тем, что тепловая мощность плазменной струи меняется пропорционально току, а при увеличении расхода газа происходит дополнительное обжатие струи, вызывающее рост температуры плазмы [2, c. 51].
К числу выходных параметров процесса плазменной обработки относятся:
- твердость упрочненного слоя;
- геометрические параметры упрочненной зоны (глубина и ширина);
- качество упрочненной поверхности (шероховатость и волнистость);
- остаточные напряжения в упрочненном слое;
- градиентное строение упрочненной поверхности, обеспечиваемое чередованием упрочненных и неупрочненных участков (табл.1).
Таблица 1.
Выходные параметры технологической системы плазменного упрочнения
Наименование группы параметров |
Параметры |
Параметры упрочненной зоны |
Твердость |
Глубина |
|
Ширина |
|
Шероховатость |
|
Параметры упрочненной поверхности |
Остаточные напряжения Градиент |
Для выбора оптимальной технологии плазменного поверхностного упрочнения проводили исследования образцов из высокоуглеродистой стали на износостойкость при различных режимах и вариантах нанесения зон закалки (без зазора между зонами и с зазором – градиентного упрочнения). Была достигнута твердость 50….55 HRC, размеры упрочненной зоны: ширина 10..12 мм и глубина 1,0 …1,2 мм. Упрочнение выполняли по трем схемам: упрочнение без зазора, упрочнение с зазором, равным половине ширины зоны упрочнения вдоль направляющих и с таким же зазором под углом 450 к направлению продольной подачи. Установку расстояния от среза сопла плазматрона до упрочняемой поверхности и выбор угла наклона при упрочнении наклонных поверхностей осуществляли вручную [3, с. 24].
Результаты испытаний стойкости направляющих после поверхностного упрочнения показали, что градиентное плазменное поверхностное упрочнение позволяет увеличить износостойкость направляющих в 2,5…2,9 раз и тем самым увеличить межремонтный интервал. При этом градиентное нанесение упрочненных зон позволяет получить благоприятное расположение полей остаточных напряжений. Образовавшиеся в процессе приработки впадины на неупрочненных участках служат в качества масляных карманов, что, в свою очередь, улучшает условия работы обрабатываемой детали[4, с. 194].
Выводы
1. Определено, что основными регулируемыми параметрами процесса плазменного поверхностного упрочнения являются максимальная температура нагрева поверхностного слоя Тнаг.и скорость охлаждения поверхностного слоя vохл. При этом эти параметры Тнаг и vохл. не являются параметрами прямого регулирования при разработке технологии плазменного упрочнения, а являются комплексными параметрами, на значения которых влияют большое число факторов.
2. Для создания интегрированных технологических процессов упрочнения деталей рекомендуется системный подход к анализу влияния входных и выходных параметров процесса плазменной поверхностной обработки с нанесением упрочненного слоя градиентного строения на характеристики упрочненных изделий.
3. К числу входных параметров технологической системы отнесены параметры плазменной обработки, движения детали или плазматрона, параметры обрабатываемого материала. К выходным параметрам поверхностной плазменной обработки отнесены: твердость упрочненного слоя, геометрические параметры упрочненной зоны (глубина и ширина), качество упрочненной поверхности (шероховатость и волнистость), остаточные напряжения в упрочненном слое и градиентное строение упрочненной поверхности, обеспечиваемое чередованием упрочненных и неупрочненных участков.
